Willkommen bei X-Net
Unsere Mission: Open Source als IT-Standard etablieren.
Keine X-beliebige
IT- und OT- Dienstleisterin
Wir begeistern unsere Kund*innen mit unseren Services wie IT-Systembetreuung, Hardware-Entwicklung oder Netzwerksupport. Dabei liegt unser Fokus auf individuellen Speziallösungen. Offen sind wir nicht nur im Hinblick auf die Technologie, sondern auch im menschlichen Umgang: Diversität, respektvolles Miteinander und partnerschaftliche Zusammenarbeit sind uns wichtig. Überzeugen Sie sich bei einem gemeinsamen Projekt davon!
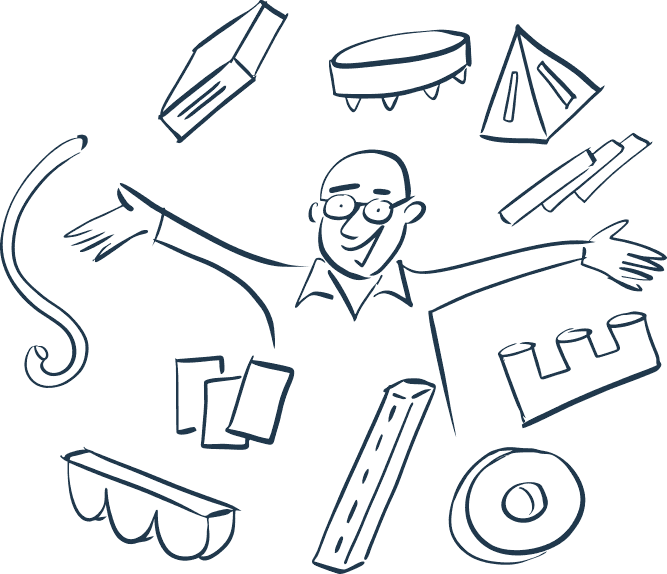
Können wir
Der Open Source Gedanke treibt uns an.
Größtmögliche Unabhängigkeit:
Wir setzen uns für Datensouveränität ein.
Wir machen Innovationen gemeinsam nutzbar.
Wir verbinden Menschen und Disziplinen mit maßgeschneiderten Individuallösungen.
Arbeiten mit ganz viel Vielfalt.
Arbeiten bei X-Net bedeutet, Teil eines vielfältigen Teams zu sein, das gemeinsam innovative und nachhaltige Lösungen entwickelt. Bei uns findest du eine offene, inklusive Kultur, in der jede einzelne Person zählt und Ideen gehört werden. Ob du an individuellen Technologieprojekten, der Realisierung von sicherer Kommunikation oder in der Analyse von Biodaten arbeiten möchtest – wir setzen auf das Miteinander und die Stärken jedes Individuums, um Großes zu erreichen. Bei X-Net verbindet uns der Wille, gemeinsam eine sichere und nachhaltige digitale Zukunft zu gestalten. Werde Teil unseres Teams und bringe deine Perspektive mit ein!
Weil Entwicklung auch Forschung braucht.
Wir bei X-Net entwickeln nachhaltige, langlebige Produkte, die ressourcenschonend gewartet werden und immer den höchsten Sicherheitsstandards entsprechen. Durch Open Source und unsere nie enden wollende Neugier treiben wir innovative und individuelle Lösungen voran und optimieren unsere Dienstleistungen.
Jedes Unternehmen ist einzigartig. Genauso wie unsere maßgeschneiderten Projekte. Wir decken ein breites Spektrum ab, von der Prävention vor Fake-Shop Käufen bis zur sicheren Datenbereitstellung entlang einer Supply Chain. Die Projekte bauen auf einer fundierten Forschungsbasis auf, die Innovation und Effizienz vereint.